SAP Business One In-Depth Review: Production Module
In the article below, we explore such a substantial element of SAP Business One as its Production module. The following blog post highlights three topics: Bill of Materials, Resources, and Production Orders. What’s hidden behind these terms? Who uses the SAP Business One Production module? Is it possible to automate production workflow management? You will find the answers below.
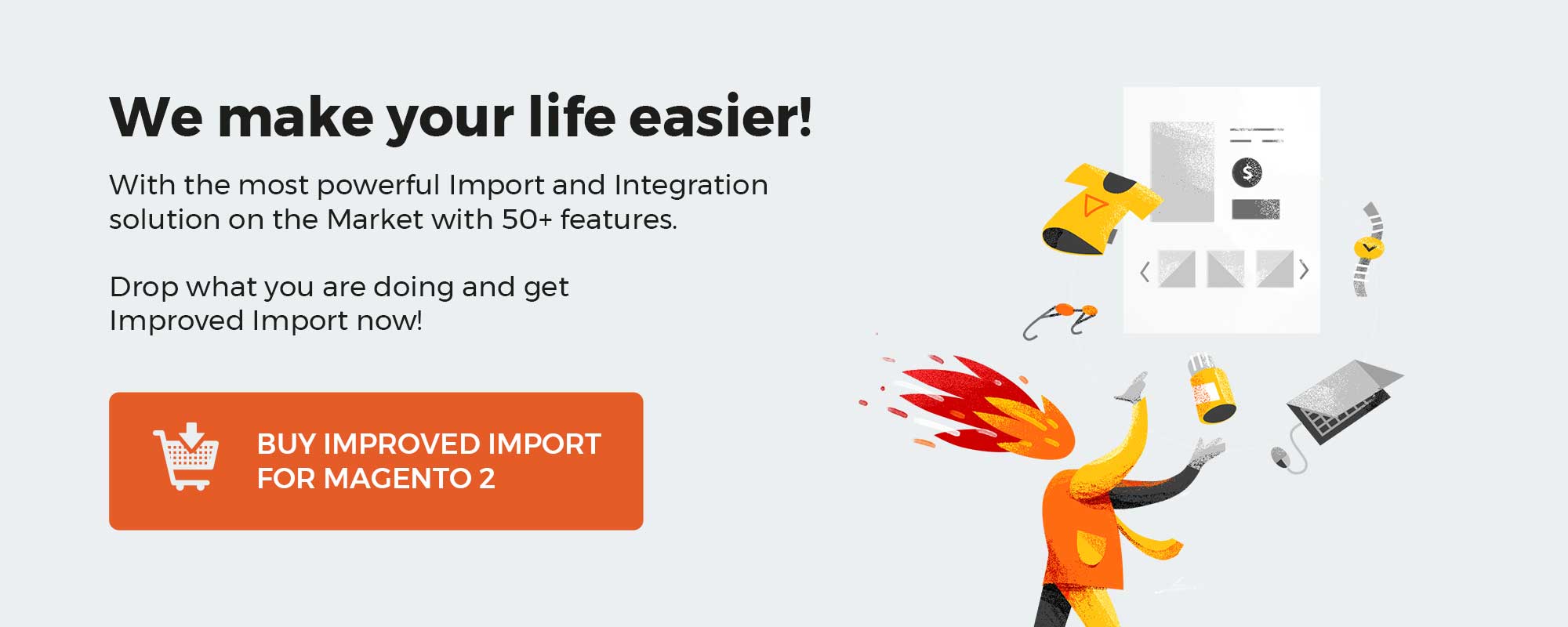
Table of contents
- 1 SAP B1 Production Module Essentials
- 2 How to integrate SAP Business One with external systems
- 3 SAP Business One Integration FAQ
- 3.1 How to connect SAP Business One to Magento 2?
- 3.2 How does the integration work?
- 3.3 Is the Magento 2 SAP Business One integration connector an open-code solution?
- 3.4 Does it offer real-time synchronization?
- 3.5 Can I manage Magento 2 data in the SAP Business One UI?
- 3.6 Which SAP entities can be synchronized with Magento 2?
SAP B1 Production Module Essentials
Let’s see why the production module of SAP Business One is useful and who can leverage it. If your company does light assembly or sells items in bundles, this tool can dramatically simplify your daily routine. First of all, you need to treat a bill of material in a special way.
SAP Business One provides the ability to specify y a top-level item. Some SAP users refer to it as a finished material or parent. Next, you have to decide what components are child items. After that, take the production order and bring everything together, producing the corresponding parent product from its components. That’s it!
However, this process is way more detailed, so we need to shed light upon several important nuances, such as types of bills of materials used in SAP Business One.
Bill of Material Types
SAP Business One offers the following four BOM types:
- Sales. It is a sales document bill of material with a strict requirement to follow: its parent item must be a sales item. Let’s assume that you sell a gift package. It is a bundle item that contains multiple products. SAP Business One provides the ability to set it up as a sales bill of materials. The package (bundle) gets the parent item name. As for the child items, they are the inventory items inside the package. How does SAP Business One help to manage such products?
Once the parent item is specified in a sales document, the corresponding child items appear as sub-items. Although you get the ability to update information about parent and child items, such as quantity, it is impossible to remove child items or add new sub-items to the package right in the sales document.
Another important aspect is related to the visual representation of your sales documents. SAP Business One enables you to hide BOM components for printing when you set up the BOM. Consequently, only the parent item is represented when you print the document.
As for the gross profit for a sales BOM, SAP Business One calculates it for the child items. - Assembly. This BOM is almost identical to the one we’ve just described. The only difference is that its child items are not represented in the sales document. You can view only parent items there. However, when such documents appear in the system, SAP Business One updates the inventory level of the child items automatically.
It is also worth mentioning that the system takes the base price for the gross profit calculation from the sum of the child items’ base prices. You can view it in the parent item’s row. - Template. If you need a BOM with no restrictions, consider using this one. It supports any item type for both parent and child items. You can delete, add, or duplicate rows and make any modifications. Consequently, it is possible to use BOM templates in sales and purchasing documents for a wider variety of purposes.
- Production. Use this BOM type in the production order document where a parent item is a finished good while child items are its components. SAP even lets you add labor as a component as a non-inventory item that has a standard cost.
In addition to the features described above, SAP Business One provides the ability to manage BOMs in bulk. Go to the Production main menu and you will discover the following two instruments:
- Update Parent Prices Globally. This instrument provides the ability to update parent item’s price following new prices for its child items. SAP Business One analyses price lists to identify components with new prices. Next, it recalculates a new price for the parent component.
- Bill of Materials – Component Management. With the aid of this instrument, you can initiate transactions that change, delete, or add BOM line items, updating the existing BOMs. Let’s assume that you no longer add a specific item to several bundle products. SAP lets you remove it from all of them in bulk.
You can apply additional configurations to sales BOM prices. SAP Business One provides the ability to choose a basis for their calculation under Administration -> System Initialization -> Document Settings -> General tab. Here you can specify whether to configure the sales prices from the parent item to its children.
Watch how to create a new BOM below:
Resources
Resources represent a special type of master data utilized in the production processes. Under this term, we consider such resources used in the production as labor hours, machine capacity, other means, etc.
You should manage SAP Business One resources as follows:
- Create the resource master data;
- Link it to the BOM or production order via the Resource row type;
- Define the resource master data: its key piece of information is the capacity that displays the availability of resources by date (e.g., hours of labor available on a certain day).
The resource master data window displays the resource number, description, type, group, measure units, etc. Other information is split between the following tabs:
- General – this tab contains information about the resource issue method, allocation, linked item, and cost;
- Capacity Data – this tab displays capacity data per warehouse for a particular period;
- Planning Data – this tab shows daily capacity factors;
- Employees – this tab provides information about employees associated with this resource;
- Properties – this tab contains resource properties;
- Attachments – this tab stores attachments associated with the resource;
- Remarks – this tab offers all remarks related to the resource.
The resource master record displays the resource availability per the warehouse. The General tab of the resource master data lets you add up to 10 costs that compose the total resource cost. This parameter is used for calculating and posting component costs. Note that it is necessary to specify primary accounts for resource expenses and WIP in the G/L account determination to enable the correct functionality for these processes.
You can select the Internal Resource Capacity option from the context menu to update the daily capacity of the defined period. Proceed to the Planning Data tab of the resource master data record. Here, SAP Business One provides the ability to specify the estimated daily capacity for each day of the week. For instance, your daily capacity for 3 employees that work 8 hours a day is 24 hours.
Production Order
SAP Business One utilizes the production order documents to record the finished materials to be produced along with their components and issue methods. The system offers two ways of creating POs. Firstly, you can run through all the corresponding processes manually. Secondly, the system lets you leverage the Procurement Confirmation Wizard to automate this process.
By default, the following three types of POs are at your service:
- Standard. With this type, components are issued while the corresponding parent is received. It is based on a production BOM.
- Special. Components are also issued while the corresponding parent is received. The parent item can be any inventory item while components are specified individually.
- Disassembly. This type works in the opposite direction: the parent item is issued while child items are received. It is based on a production BOM as well.
If you need to add a production order in SAP Business One, follow these steps:
- Choose the production order type;
- Specify the parent item.
- Set the parent item quantity.
- Specify the production order due date (the production completion date).
- Assign a sales order (optionally).
- Depending on your BOM setup, components appear automatically. Add/delete them.
- Configure other parameters, such as the base quantities, warehouse, issue method, etc.
- Now, you can add the production order.
Don’t forget to change the status of your PO to Released when the production process begins. From the context menu, and choose the Issue Components option to add manual components. Report the completion of production at the end of the process to receive the finished item into stock. Also, this action triggers the cost of producing the item.
Also, note that items set to backflush are issued automatically. You only need to choose Report Completion. SAP Business One creates an Issue for Production document automatically. However, it is impossible to backflush items that are managed with serial numbers or batch numbers. They are bound to a manual issue method so that you have to identify the serial numbers or batches to release them from inventory.
As for the Summary tab, it displays the components’ total cost, finished goods cost, and whether any variances between them occur for the standard costing method. Changing the production order status to Closed triggers the variance posting to the WIP variance account. Note that for Moving Average, FIFO, or Serial/Batch valuation methods, SAP Business One updates the parent cost on the basis of the component’s total cost.
You can see more information about production orders below:
How to integrate SAP Business One with external systems
SAP Business One is almost a perfect ERP system except for several nuances. It still has some drawbacks when it comes to fully-featured integration with e-commerce platforms which is a questionable task. However, getting the missing functionality is only a matter of a few clicks. You need a third-party connector that enables SAP integrations with core e-commerce platforms, such as our tools for Magento 2 and Shopify. Don’t hesitate to contact us for further information on the SAP Business One integration with your business and check our SAP Business One Integration solution for Magento 2.
SAP Business One Integration FAQ
Below, you will find more information about our SAP Business One Magento 2 connector.
How to connect SAP Business One to Magento 2?
As we’ve already mentioned above, you need a third-party solution to connect SAP B1 to Magento 2. With our SAP Business One Integration tool, you get the ability to connect your Magento 2 website with SAP Business One. The extension lets you transfer data between the two platforms using multiple API connections.
How does the integration work?
The SAP Business One Integration tool creates a data flow between your Magento 2 website and SAP Business One, syncing the two systems with the help of multiple API connections. Also, it uses a cron scheduler to automated data transfers and a robust mapping interface to prevent issues caused by different data storage standards.
Is the Magento 2 SAP Business One integration connector an open-code solution?
Our connector always was and always will be an open-code solution. We let you change it according to your preferences and business needs.
Does it offer real-time synchronization?
The Magento 2 SAP Business One connector provides the ability to transfers most changes in real-time. The exchange happens right after you edit any entities or update master data.
Can I manage Magento 2 data in the SAP Business One UI?
The connector lets you manage products, orders, customers, categories, and other Magento 2 entities right in the interface of your SAP B1 installation. Next, it transfers all the changes to your e-commerce store.
Which SAP entities can be synchronized with Magento 2?
You can transfer the following SAP Business One data: Item groups, Items, Price List, Period Discounts, Volume Discounts, Inventory Data, Discount Groups, Discount Groups, Customer Groups, Business Partners, Sales Orders, Deliveries, Business Partners, Business Partner Contacts. The connector also works with all the core Magento 2 entities.
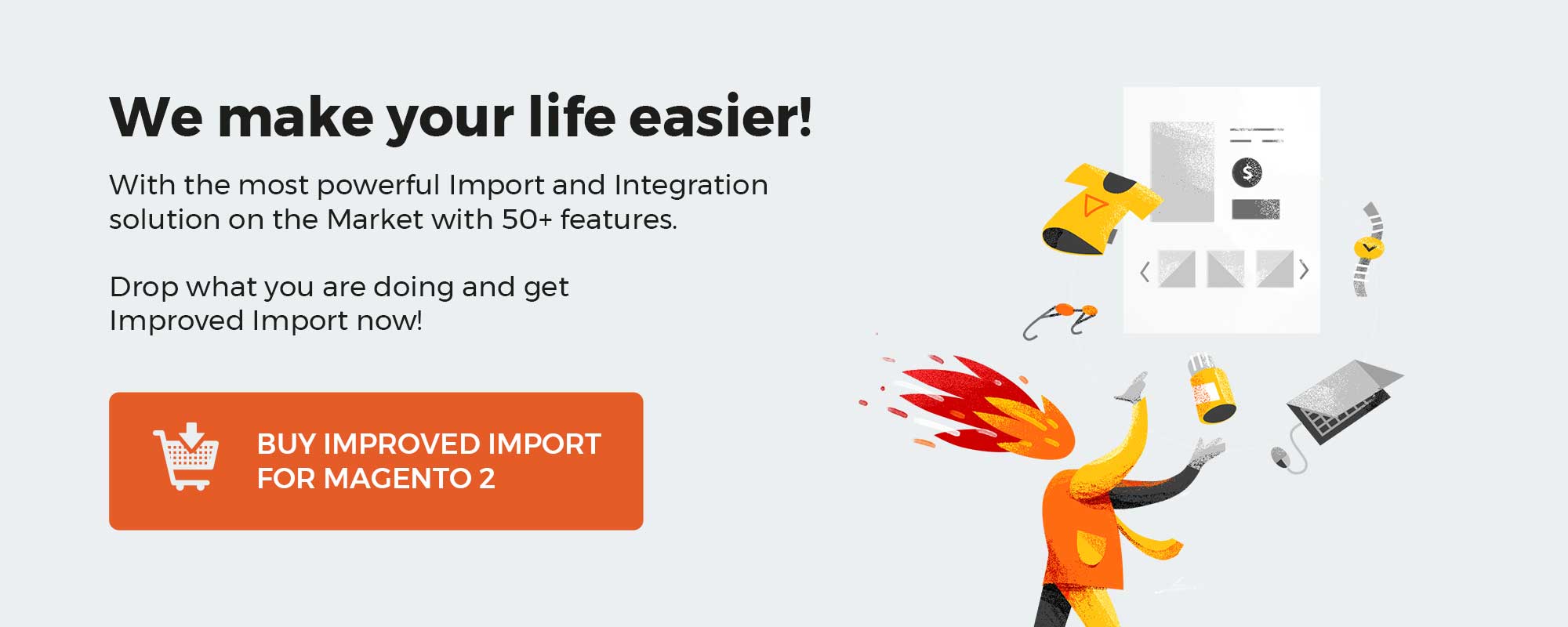